Overview
The Fender Rhodes Piano is a unique electro-mechanical keyboard instrument, designed to produce sound via the interaction of hammers and metal tines, which are then amplified electromagnetically. Unlike a traditional acoustic piano, the Fender Rhodes’ construction relies on intricate engineering involving precisely calibrated components, each of which contributes to its signature tone. The instrument was produced in large-scale manufacturing facilities, with attention to detail in its mechanical components and electrical systems.
Factory Production Process
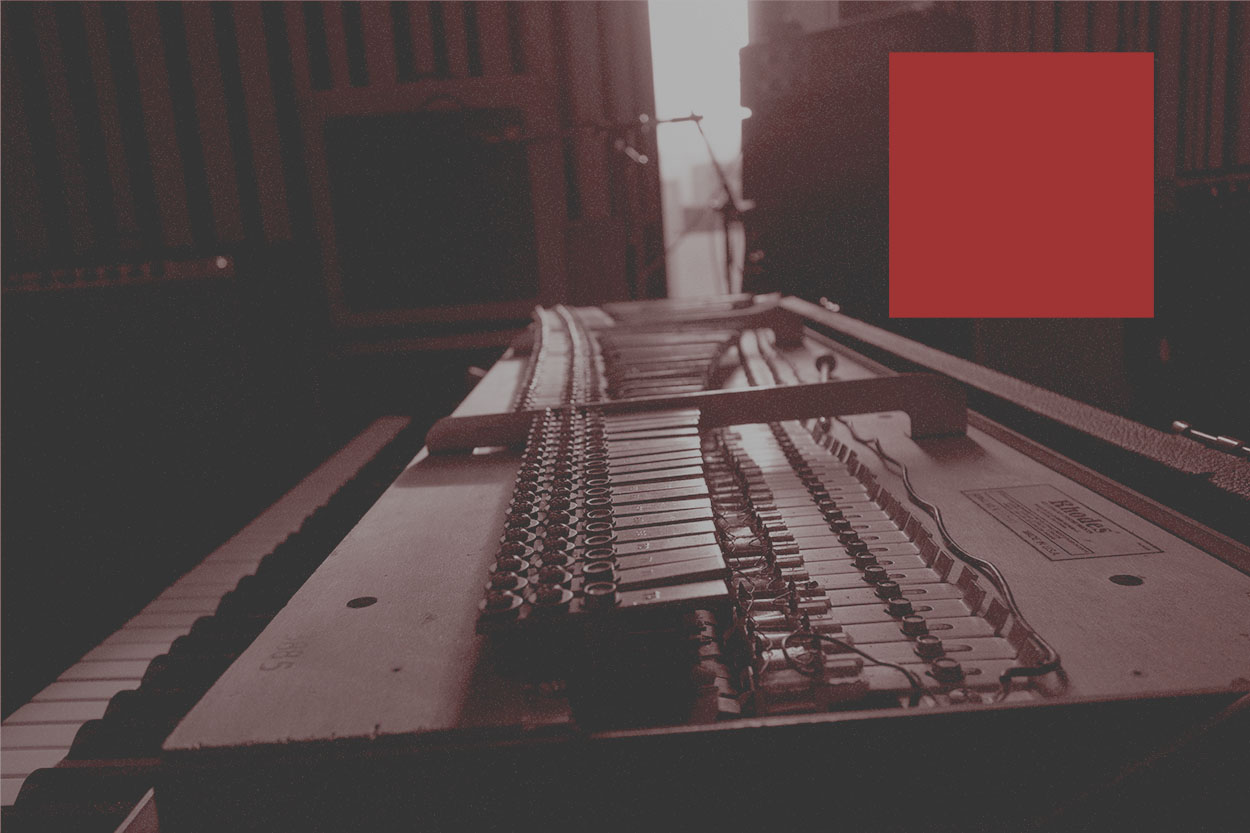
The Silk Rhodes: Redefining the Classic Fender Rhodes Experience
The manufacturing process for the Fender Rhodes piano took place in dedicated facilities, particularly during the height of its production in the 1960s and 1970s. The process began with the assembly of the instrument’s key components, including the tine assembly, the tone bars, and the hammer mechanism. These components were produced with strict tolerances to ensure proper tonal quality and mechanical consistency.
The factory workflow consisted of several stages:
- Raw Material Preparation: Tines, typically made from a durable steel alloy, were precision-cut to specific lengths depending on the pitch. The factory ensured that the material properties, such as hardness and flexibility, were maintained to achieve consistent vibrations.
- Tone Bar Calibration: Each tine was paired with a corresponding tone bar, which is a weighted metal bar that reinforces the vibration of the tine. The tone bars were carefully tuned in the factory by adjusting their mass, typically by adding or removing solder to achieve the desired pitch stability and sustain characteristics.
- Hammer and Damper Assembly: The hammer mechanism closely resembles that of an acoustic piano but instead strikes the tine rather than a string. The factory’s production line used a system to align and calibrate each hammer to ensure that they produced a uniform dynamic response across the keyboard range. Each hammer is also paired with a damper mechanism to control note decay.
- Electromagnetic Pickup Installation: After the mechanical components were assembled, electromagnetic pickups, similar to those in electric guitars, were installed near each tine. The positioning and alignment of these pickups were critical for sound clarity, and each pickup was wired to ensure proper amplification of the tine’s vibrations.
Mechanical Operation
The operation of the Fender Rhodes relies on a combination of mechanical actions and electromagnetic principles. When a key is pressed, it triggers the following sequence of actions:
- Hammer Strikes the Tine: The key activates a lever mechanism that propels a felt-covered hammer towards a metal tine. The force applied to the key determines the velocity of the hammer, which in turn affects the volume and tonal attack of the note.
- Tine Vibration: When the hammer strikes the tine, it induces vibration at a frequency corresponding to the tine’s length and thickness. Shorter tines produce higher-pitched notes, while longer, thicker tines vibrate more slowly, producing lower notes.
- Tone Bar Resonance: Attached to each tine is a tone bar, which helps amplify the vibration. The tone bar acts as a resonator, extending the sustain and modifying the harmonic content of the note, giving the Rhodes its characteristic “bell-like” sound.
- Pickup Electromagnetic Interaction: As the tine vibrates, it moves through the magnetic field of the electromagnetic pickup. This motion induces a current in the pickup coil, creating an electrical signal that corresponds to the tine’s vibration pattern. This signal is sent through the instrument’s output circuitry, where it can be further modified by effects or amplification.
One of the critical factors in the Rhodes’ design is the tine’s relationship with the pickup. Adjusting the distance between the tine and the pickup alters the tonal characteristics of the sound. Closer proximity yields a brighter, more percussive sound, while increasing the distance results in a softer, more mellow tone.
Electrical and Amplification System
The Rhodes piano operates using passive electromagnetic pickups, similar to those found in electric guitars. The signal generated by the pickups is routed through the instrument’s output jacks, where it can be sent to external amplification systems. The most common choice for amplifying the Rhodes piano was the Fender Twin Reverb amplifier, which added depth and warmth to the instrument’s sound.
The instrument was often paired with effects such as tremolo, phasers, or reverb to further shape its sonic characteristics. In some models, onboard effects were integrated into the design. For instance, the Rhodes Suitcase model included a stereo tremolo effect, which panned the sound between two speakers, creating a spatially immersive experience.
Technical Adjustments and Maintenance
Technicians working with Rhodes pianos often had to make fine mechanical and electrical adjustments to optimize performance. Common adjustments include:
- Tine and Pickup Alignment: The tine’s position relative to the pickup is crucial for proper tonal balance. Technicians often had to manually adjust the angle and distance of the tine to achieve the desired sound.
- Hammer Tension Calibration: The hammers were typically spring-loaded, and the spring tension could be adjusted to affect the hammer strike force and dynamic response.
- Tuning: Unlike acoustic pianos, where tuning is done by adjusting string tension, Rhodes pianos are tuned by adjusting the length of each tine, typically by filing or trimming the tine to adjust its frequency.